Это первая статья из серии. В ней мы расскажем:
- как организовать производство под заказ и в свободный остаток;
- как разгрузить директора по производству;
- в каких случаях разрыв цикла – не ошибка, а стратегия;
- как типовыми средствами 1С решать задачи, связанные с переработкой и давальческим сырьём;
- каким образом включить непроизводственных сотрудников в производственный цикл без потери эффективности.
1. Как организовать производство под заказ и в свободный остаток?
Организация производства – одна из ключевых зон развития для производственных компаний. Особенно остро вопрос организации встаёт, когда компания работает под заказ. Ведь у неё возникают сложности: не удаётся точно определить сроки исполнения заказа, трудно внести правки в график приоритетов при поступлении срочного заказа, а при наступлении форс-мажора (например, поломке оборудования или задержке поставок) нет возможности оперативно принять управленческое решение.
1.1. Управление очередью заявок при производстве под заказ
В производственном контуре 1С:ERP предусмотрены механизмы как для выпуска продукции под конкретные клиентские заказы, так и для производства в свободный остаток. Первый вариант – характерен для нестандартизированной продукции, при высоких требованиях к индивидуализации. Второй применяется при регулярном спросе на типовую продукцию – тогда целесообразно накапливать её на складе.
Главные сложности в производстве под заказ: определение даты готовности продукции и управление приоритетами. В качестве решения здесь будет полезен инструмент «Расчёт графика производства». Это типовой инструмент 1С:ERP, который позволяет формировать производственную очередь, учитывая ряд параметров:
- Срочность заказа – система автоматически повышает приоритет срочных заказов.
- Желаемая дата исполнения – при её наличии система учитывает пожелания клиента.
- Длительность этапов – все расчёты строятся с точностью до часов и минут.
- Загрузка оборудования – учитывается работоспособность и загруженность рабочих центров.
- Обеспеченность материалами – если для реализации этапа не хватает сырья, система может снизить приоритет или вовсе исключить этап из очереди.
Благодаря этому инструменту, место каждой позиции в очереди становится результатом объективного анализа текущей ситуации в производстве. Например, если на 7 марта запланирован заказ с длительностью выполнения 15 рабочих дней, система рассчитывает его готовность на 00 часов 00 минут 27 марта.
Однако с учётом текущей загрузки оборудования реальная дата исполнения может быть обозначена системой как 23 часа 59 минут 28 марта, с автоматическим указанием опоздания (в данном случае – 48 часов).
Этот типовой инструмент становится ответом, который помогает принять управленческое решение: когда и какие заказы мы сможем выполнить, какой новый заказ сможем принять, не нарушая текущих сроков.
1.2. Производство в свободный остаток: как спрогнозировать загрузку
Возможность формирования производственной очереди позволяет оперативно принимать решения в условиях изменяющейся загрузки. Когда поступает срочный заказ, можно автоматически пересчитать график, понять, какие заказы можно сместить, заранее уведомить клиентов. Благодаря этому планирование становится не субъективным ручным процессом, а управляемым и прозрачным инструментом.
Однако когда речь идёт о производстве в свободный остаток – когда нет заказов клиентов и заказов на производство, продукция типична, и мы определяем её объём по плану продаж – типовая задача меняется. Звучит она так: не допустить простоя оборудования, избежать перерасхода ресурсов, обеспечить стабильный выпуск под прогнозируемый спрос.
Для этого в 1С:ERP применяется связанная схема:
Сначала, используя данные статистики совершённых ранее продаж, формируется план продаж.
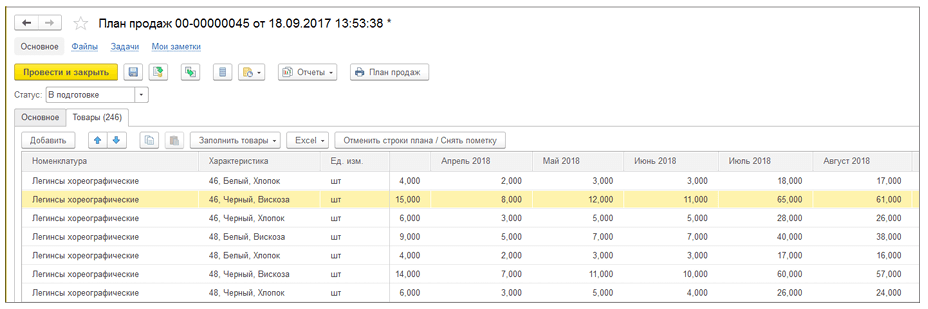
На его основании, используя заданные зависимости и формулы, система строит план производства.
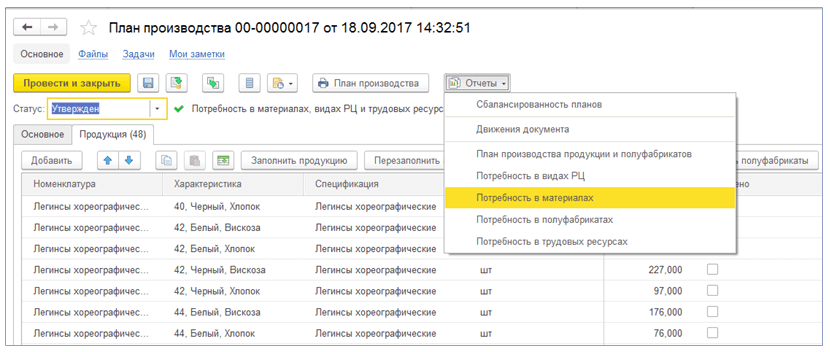
Далее, основываясь на составе изделий и спецификации, формируется план потребности в материалах. Благодаря ему можно проанализировать, какие материалы и в каком объёме потребуются в конкретный период. Система учитывает параметры закупки, начальные остатки и помогает рассчитать, что и в какой момент времени нужно приобрести.
Такая схема позволяет выявить дефициты, своевременно скорректировать планы, превратить потребности в конкретные закупочные позиции. Это обеспечивает стабильную загрузку производства, оптимальный складской запас и предсказуемость в операционном управлении.
2. Как разделить и передать часть работы директора по производству?
Во многих производственных компаниях директор по производству оказывается перегружен. Особенно это заметно на примере средних и малых предприятий, где на одного человека замыкается сразу несколько ключевых функций: от планирования и диспетчеризации до оперативного контроля исполнения. Такая концентрация задач тормозит процессы, снижает управляемость и делает компанию уязвимой: если директор по производству увольняется или временно теряет трудоспособность – рабочие процессы буквально «встают».
2.1. Выделение части обязанностей в отдельную роль диспетчера
Первый шаг в решении этой бизнес-задачи – разделить роли. По нашему опыту, наиболее эффективный вариант – разделить роли диспетчера и директора по производству. Это два разных уровня: диспетчерская работа – преимущественно исполнительского характера. Она не требует управленческих компетенций, а значит, может быть делегирована сравнительно легко и в рамках небольшого бюджета.
Выделенный диспетчер занимается задачами по управлению производственной очередью. В типовом функционале 1С:ERP для этого предусмотрено специальное рабочее место – «Диспетчирование». В нём отображается:
-
перечень заказов на производство, вне зависимости от источника (продажи, план продаж, ручной ввод);
-
очерёдность исполнения заказов, рассчитанная системой;
- распределение заказов по цехам, рабочим центрам и исполнителям.
2.2. АРМы для эффективного распределения ролей
Подробнее о том, как в точности работает механизм распределения ролей через АРМы, который помогает разгрузить директора по производству.
-
Диспетчер отвечает за поступившие заказы на производство и контролирует их очередь. Как было сказано ранее, он работает в АРМ «Диспетчирование»: анализирует текущую загрузку, пересчитывает приоритеты, определяет порядок выполнения заказов. И лишь при возникновении нестандартной ситуации (форс-мажоры, срочные заказы) диспетчер взаимодействует с директором по производству для совместного принятия решений.
-
Мастер смены или мастер цеха является фактическим исполнителем. Он получает перечень работ по этапам (в установленном порядке), закреплённым за его участком. И обеспечивает их выполнение. После «физического» завершения работы мастер фиксирует результаты в системе, указывая фактический расход материалов. Для этого предусмотрен АРМ «Этапы производства, отметки факта».
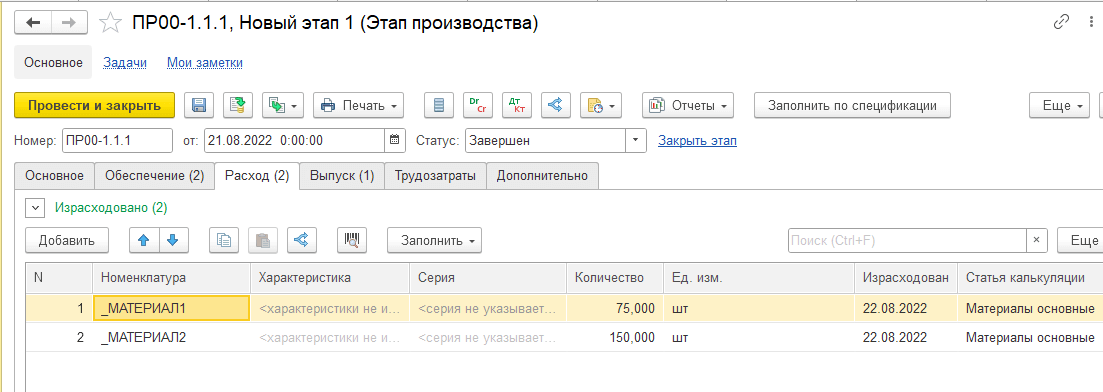
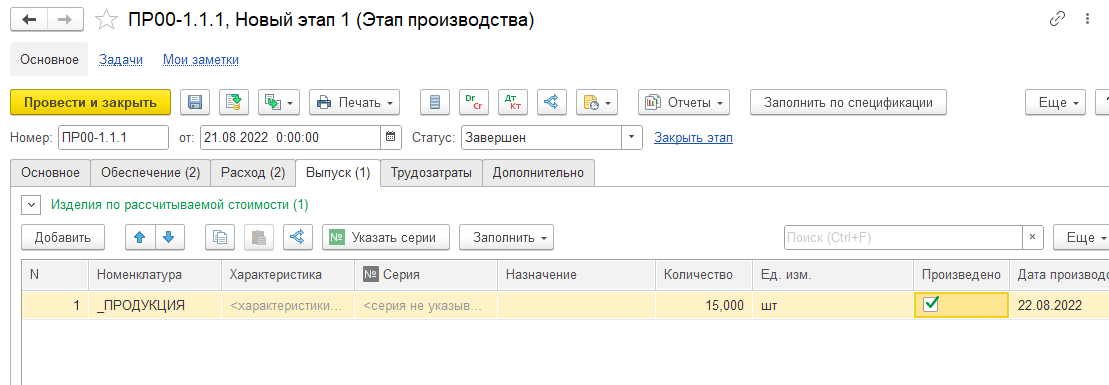
- Производственные рабочие (сборка, покраска, сварка и т.д.), в свою очередь, работают через АРМ «Выполнение операций». В нём отображаются конкретные задачи, поставленные перед каждым сотрудником. Таким образом обеспечивается прозрачность и управляемость исполнения на каждом уровне.
Благодаря системе распределения ролей и автоматизации рутинных задач, директор по производству получает возможность сосредоточиться на стратегических вопросах. Также это снижает для него риск выгорания, повышает устойчивость производственной системы на случай, если директор по производству по тем или иным причинам «выпадет» из рабочего процесса.
3. Разрывать производственный цикл – это нормально?
Изначально идея разрыва производственного цикла – когда мы делим производство одной готовой продукции на два обособленных производственных цикла – может показаться противоестественной. Привычно стремиться к непрерывному, поточному процессу, когда каждый этап следует за предыдущим без задержек. Однако практика показывает: зачастую сознательное разрывание цикла в 1С не только оправдано, но и выгодно. Рассмотрим, при каких условиях намеренный разрыв производства – хорошая стратегия, и какие инструменты помогают извлечь из этого выгоду.
3.1 Что влияет на непрерывность и почему разрывы неизбежны
На стабильность производственного цикла влияет не только очередь заказов, но и наличие комплектующих, полуфабрикатов, материалов. Часто начало или завершение этапа тормозится из-за задержки поставок или нехватки ресурсов на складе. Возникает вопрос: стоит ли прервать выполнение текущего заказа или этапа, чтобы подождать материалы – нужно ли в это время переключиться на другой заказ?
Ключевое условие непрерывности – своевременное обеспечение. Это достигается через эффективное планирование закупок и оперативное диспетчирование. Именно в этих зонах возможны точки оптимизации.
В типовой конфигурации 1С:ERP реализован инструмент «Состояние обеспечения заказов». Он позволяет отслеживать потребности по заказам, выделять их цветовой индикацией и оперативно выполнять действия с этапами.
Помимо типовых решений, эффективно разделить производственный цикл позволяют точечные доработки. Рассмотрим их на примере нескольких кейсов из нашей практики.
Кейс №1. Круглосуточное безостановочное производство
Клиент – консервный комбинат с круглосуточным производством в три смены. Перед нами стояла задача: обеспечить плавную передачу смен без сбоев, связанных с нехваткой материалов. В качестве решения в дополнение к типовому инструменту нами была сделана доработка – АРМ «Старшего мастера». Теперь мастер, завершая смену, может в своём рабочем месте проанализировать потребности следующей смены.
В интерфейсе программы он увидит:
- какие материалы требуются по взятым в работу этапам;
- какие остатки содержатся на складах;
- существующие резервы;
- по каким позициям есть дефицит (подсвечены красным).
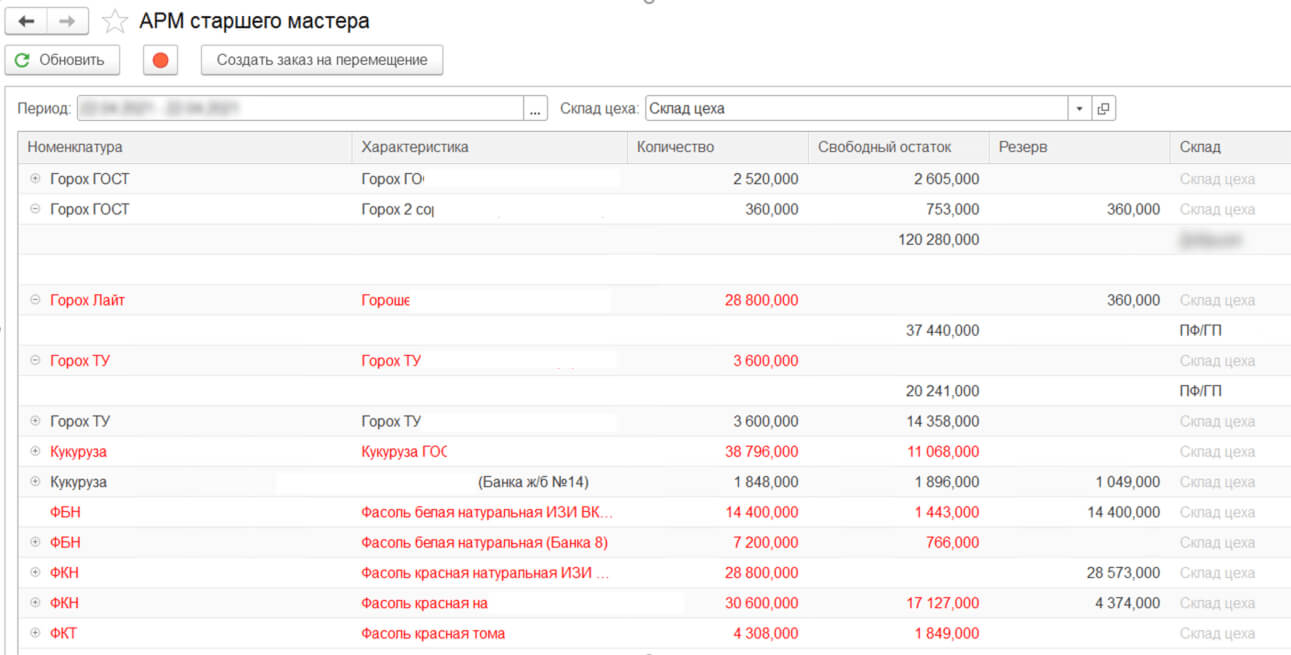
При нехватке материалов мастер может изменить очерёдность этапов, переключиться на другой заказ или инициировать перемещение между складами. Причём сделать это он может, не выходя из интерфейса, в том же окне.
Такое решение позволяет не нарушать производственный ритм, даже если какие-то позиции временно недоступны. Мастер здесь действует в роли локального диспетчера. Он не вмешивается в глобальный производственный план, но обеспечивает непрерывность на уровне смены.
Кейс №2. Производство с дефицитом одной комплектующей
Компания – предприятие по производству теплообменников. Бизнес-проблема: система не позволяет взять в работу заказ, если в наличии не все комплектующие. Однако на практике часто складывается такая ситуация: отсутствует лишь одна деталь, при этом её отсутствие не сказывается критически на дальнейшем производственном процессе. Большая часть изделия может быть собрана, и только финализация изделия зависит от этой позиции.
Поэтому нужно обойти эту сложность: чтобы система давала возможность взять заказ в работу, и лишь не давала завершить его, по причине отсутствия в спецификации последней детали.
В качестве решения проблемы мы реализовали АРМ «Обеспечение материалами». Это АРМ, где всё можно выполнить на одном экране. Он показывает:
- структуру заказа;
- потребности по каждой комплектующей;
- возможность замены на аналоги из текущего запаса.
Если деталь задерживается, а на складе есть аналог – замена происходит автоматически. При этом вся цепочка – начиная от резервирования и заканчивая корректировкой спецификации – выполняется без выхода из интерфейса.
Благодаря доработке мы получаем полноценное интеллектуальное управление обеспечением под заказ; в котором система позволяет принять гибкое решение – начать производство, зная, что его завершение будет отложено.
Кейс №3. Осознанное разделение цикла на производстве
Иногда разделение производства одной готовой продукции на два производственных цикла – полноценная осознанная стратегия.
Компания – консервный комбинат. Производственный цикл здесь состоит из двух крупных этапов: непосредственное производство продукта и его упаковка. Эти процессы проходят в разных цехах, с разными сроками исполнения и материалами.
Было принято решение: выделить два самостоятельных производственных процесса. Первый – производство полуфабриката (неупакованного) без привязки к конкретному заказу. Второй – упаковка под конкретный клиентский заказ. Такой подход позволил:
- управлять загрузкой цехов отдельно;
- снять зависимость одного этапа от другого;
- ускорить отгрузку по готовности упаковки.
Также был разработан специальный АРМ, в котором отображаются:
- дата отгрузки и менеджер заказа;
- наименование готовой продукции и используемый полуфабрикат;
- необходимое и запланированное количество;
- статус наличия компонентов (ПФ, этикеток, стикеров);
- ссылка на клиентскую заявку.
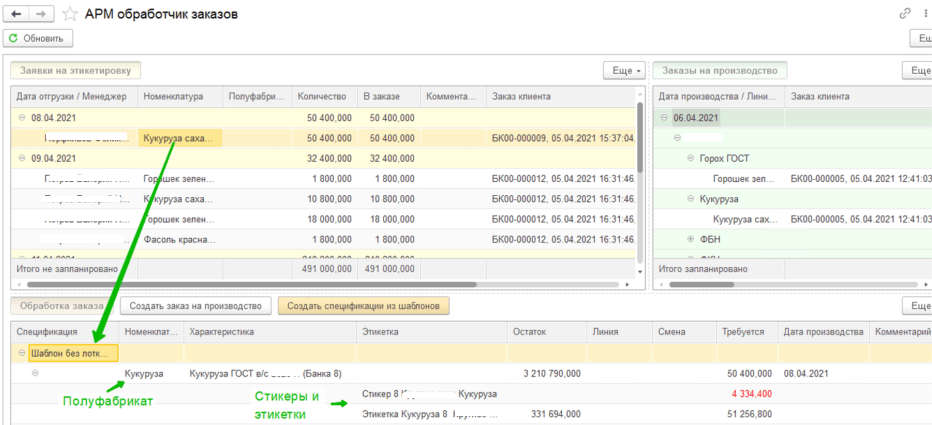
Из этого же интерфейса можно:
- создать заказ на упаковку;
- откорректировать спецификацию (например, заменить стикер или наклейку);
- инициировать выполнение нового этапа.
Таким образом разрыв даёт возможность синхронизировать производственные ресурсы с клиентским спросом, в отличие от работы по типовому сценарию.
4. Как работать с давальцами и переработчиками?
Использование давальческого сырья и привлечение внешних переработчиков – схемы работы, которые часто встречаются на ряде производственных предприятий. Эти схемы полностью реализованы в типовом решении 1С:ERP: начиная с учёта материалов и заканчивая автоматизацией документооборота и отражения в бухгалтерии.
4.1 Реализация давальческой схемы: автоматизация ключевых процессов
Схема работы с давальцами предполагает, что заказчик предоставляет своё сырьё (полностью или частично), а предприятие производит из него готовую продукцию. В типовом решении 1С:ERP для этого реализованы все ключевые процессы:
-
Учёт движения сырья и материалов – поступление давальческого сырья и его расход при производстве. Также контролируется возврат в виде готовой продукции.
-
Контроль остатков – точный учёт остатков давальческого сырья на складах. Особенно важен при параллельной работе с несколькими клиентами.
-
Расчёт себестоимости – учитываются все затраты на переработку, в том числе трудозатраты, эксплуатация оборудования, энергия и прочее. Позволяет корректно рассчитывать себестоимость готовой продукции.
-
Управление договорами – полный учёт условий: от передачи сырья до возврата готовой продукции.
- Автоматизация документооборота – упрощённое создание всех необходимых документов: актов приёма-передачи, отчётов о переработке, сопроводительных накладных и иных документов. Все документы содержат необходимые проводки для отражения в 1С:ERP или 1С:Бухгалтерии.
4.2 Реализация схемы с переработчиками: автоматизация ключевых процессов
Другая схема – когда само предприятие передаёт часть операций на сторону. Например, это может быть покраска, термообработка, гальваника или сборка, выполняемая сторонней организацией. Сценарий работы с переработчиками охватывает:
-
Учёт передачи сырья – фиксируется, какие материалы и в каком объёме переданы контрагенту, включая внутренние перемещения и формирование накладных.
-
Контроль остатков – отслеживаются остатки у переработчиков, что важно для предотвращения потерь и учёта незавершённого производства.
-
Учёт возврата продукции – фиксируется возвращение готовой продукции или полуфабрикатов, с контролем на соответствие условиям договора (объём, качество, спецификация).
-
Расчёт затрат на переработку – все внешние работы учитываются с полной детализацией: стоимость услуг, транспортные расходы, материалы переработчика и т.д.
-
Управление договорами – поддерживается ведение договоров с переработчиками, включая условия поставки сырья и получения готовой продукции.
-
Автоматизация документооборота – автоматическое формирование всех документов: накладных, актов выполненных работ, документов по возврату. Документы также интегрированы в учётную систему и содержат проводки для бухгалтерии.
4.3 Почему стоит использовать типовую схему
Может показаться, что подобные схемы избыточны и громоздки, особенно при небольшой доле давальческих операций. Однако типовое решение 1С:ERP отрабатывает эти сценарии полностью – от логистики до финансов. Ключевое преимущество в полноте охвата:
- на входе – поступление от давальца или передача переработчику;
- в процессе – контроль движения, остатков, затрат;
- на выходе – отчёт о переработке, возврат продукции, закрытие этапов.
Схема надёжна, прозрачная и готова к промышленной эксплуатации без дополнительных доработок. Также благодаря автоматизации давальческую схему и схему работы с переработчиками легко масштабировать на большое число контрагентов.
5. Как включить в процесс непроизводственных сотрудников?
Не все участники производственного цикла находятся в цехах. На ряде предприятий результат производства напрямую зависит от работы непроизводственных специалистов: конструкторов, дизайнеров, проектировщиков, программистов ЧПУ. Хотя их деятельность напрямую и не относится к производственным операциям, без неё цикл не может стартовать или завершиться. В то же время у таких сотрудников есть ряд особенностей:
- отдельные руководители и структура подчинённости;
- разнородные задачи, часто без нормирования и единых стандартов исполнения;
- характер работы затрудняет её включение в типовой производственный план.
Тем не менее участие таких сотрудников можно и нужно интегрировать в производственный цикл. Это необходимо для учёта загрузки, сроков, полноты и качества выполнения. Для этого мы используем типовой объект ERP-системы – «Задача» и связываем её с этапами производственного процесса.
5.1 Подробнее о «Задаче» как элемент производственного процесса
В системе 1С:ERP можно поставить «Задачу» как на конкретного сотрудника, так и на роль. Само по себе это решение не даёт желаемого эффекта, поэтому необходима доработка: автоматическое включение «Задачи» в производственный цикл. Теперь при запуске цикла система формирует и раздаёт задачи всем участникам, которые будут задействованы в процессе производства, включая непроизводственные подразделения. Это позволяет:
- учитывать такие задачи в общей загрузке;
- фиксировать сроки выполнения;
- контролировать результат.
Задачи могут быть привязаны к разным точкам производственного цикла: чаще всего – к его началу (например, создание ТЗ, КД, написание алгоритма работы для станка), но возможны задачи и в конце (например, финальное согласование, добавление технической документации перед отгрузкой).
5.2 Реализация схемы по включению непроизводственных сотрудников на примере задачи по разработке КД
Один из типичных кейсов – задача по разработке конструкторской документации (КД). Предположим, по заказу клиента нужно произвести изделие. Заказ оформлен, известна дата отгрузки. Ещё на старте цикла системе нужно запустить этап «Разработка КД». Поэтому в системе создаётся задача, которая связана с заказом на производство. Она направляется конструктору.
Чтобы гарантировать, что работа действительно выполнена, а её результат передан на производство, мы реализуем две доработки, которые усиливают задачу механизмами контроля:
1. Файловая проверка. В задаче указываются обязательные вложения: конструкторская документация и пояснительная записка. Система не позволит отметить задачу как выполненную, если файлы (или ссылки на макеты, если они требуют открытия в специальном ПО) не прикреплены. Это исключает ситуацию, когда формально задача закрыта, но фактически производство начать работу не может из-за отсутствия исходных данных.
2. Статус в производственном заказе. В самом заказе на производство вводится промежуточный статус. Например, «передано конструктору/проектировщику». Таким образом, даже производственный персонал, который напрямую с контролем задача не связан, может увидеть, на каком этапе находится заказ. И понять, готовы ли исходные данные для начала работы.
Использование этих инструментов позволяет:
- учитывать реальную загрузку проектировщиков и других участников до- и постпроизводственных этапов;
- интегрировать их работу в сквозной производственный цикл;
- не допускать потери времени из-за «зависших» на стороне непроизводственных сотрудников задач;
- контролировать полноту выполнения и качество результата.
Что в итоге
Эффективное управление производством в 1С:ERP строится на организационных решениях, типовых механизмах, а также точечных доработках, направленных на создание эффективных АРМов. В статье на примере реальных кейсов мы показали следующее:
- Производственную очередь можно автоматизировать, учитывая приоритеты, срочность, загруженность мощностей и обеспеченность материалами. Благодаря этому планирование становится управляемым и прозрачным.
- Производство в свободный остаток требует точности в связке цепочки планов продаж, производства и закупок. Благодаря учётной системе можно выстроить эту цепочку на основе объективной статистики.
- Перегруженность директора по производству можно устранить. Для этого необходимости выделить диспетчерскую функцию, а также использовать АРМы для мастеров и рабочих.
- Разрыв в производственном цикле может быть осознанными выбором, а не вынужденным шагом. Чтобы сохранить темп производства, необходимо обеспечить своевременное диспетчирование, гибкую работу с дефицитом материалов и продуманное разделение этапов.
- Работа с давальцами и переработчиками полностью поддерживается типовыми средствами 1С:ERP как в части логистики и планирования, так и со стороны учёта, документооборота и себестоимости.
- Включение в производственный процесс сотрудников, не относящихся напрямую к производству (конструкторов, дизайнеров и других), возможно без потери эффективность всей цепочки.
В следующих материалах мы продолжим обзор возможностей производственного контура 1С:ERP: расскажем о планировании, закупках, себестоимости, контроле качества, сервисном обслуживании, MDM и отраслевых решениях.